目前汽车制造业广泛依赖ERP(企业资源计划)和MES(生产过程执行管理系统)来打造IoT(物联网)或数字化工厂,其中ERP是顶层源数据,MES是连接系统与设备的纽带。本文以SAP(全世界排名第一的ERP软件)和camLine(德国知名MES软件)的结合应用为例,叙述二者之间的信息交互逻辑。
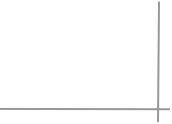
ERP系统

ERP是建立在信息技术基础上,集信息技术和先进思想于一身,以系统化的管理思想,为企业员工及决策层提供技术手段的管理平台。汽车行业应用范围最广的是SAP的ERP系统,特别是外资企业或者合资企业,如果产业链上下游都使用SAP的系统,那么可以方便订单发出和接收,实现接口的统一。以SAP为例,汽车主机厂与零部件供应商之间的需求订单可以直接由系统交互EDI(电子数据交换)完成,这样可以避免多个系统之间频繁转换带来的不便,提高数据的交互效率。
对于企业层级,ERP一般具有如下功能模块:销售订单、财务(成本核算、应收货款管理)、物料计划、供应链、生产计划、库存管理及MBOM(制造物料清单)等。在制造型企业中,往往偏重于成本核算。SAP的主要功能有商务智能、客户关系管理、企业信息管理、供应链管理、可持续性以及制造和移动等。企业层、管理层和现场(设备)层之间的垂直关系如图1所示,成本核算是本节研究的方向,是企业标准成本的年度预算制定、成本降低的重要参考依据,这些信息是ERP中存储的物料信息BOM和工艺路径信息Routine来记录的。
图 1 ERP 与 MES 的关系
对于离散型制造业来讲,成本核算一般采用标准成本法,即需要包含物料(BOM)成本和制造成本,其中制造成本进一步包含机器使用成本和人工成本(图2)。物料成本和制造成本均属于变动成本,是考核制造业运营绩效的关键指标之一。下文从物料BOM结构、物料成本管理和制造成本管理三个方面切入,浅谈三者各自的计算方法,为进一步讲解与MES的结合做铺垫。
图 2 汽车零部件成本组成
1.物料BOM结构
汽车上任何一个组合件动辄由多达数十个部件或原材料组成,它们之间往往是多层级、多来源的树形复合体,因此在SAP中广泛采用“水晶报表”来管理BOM。根据原材料的来源不同,又细分为:外购原材料、外购半成品、自制半成品和成品等。本文选取汽车电子产品中比较典型的汽车仪表进行研究,该产品工艺复杂,零件众多,由机械件、电子件和软件等三大部分组成,具有广泛代表性。
2.物料成本管理
该型号的仪表总成装配由6个装配和测试工序组成,如表1所示,列出了各个零部件的用量、物料类型和单价,以及最终成品的总成本。
表 1 仪表的物料成本
3.制造成本管理
制造成本主要由机器使用成本和人工成本两大部分组成,两者都使用“标准成本法”进行核算,即使用时间×标准成本单价。汽车行业广泛使用工艺路径来包含上述两个方面,如表2所示,以某型号汽车仪表为例。
表 2 仪表的制造成本构成
本文中提到的该型号汽车仪表成本构成示例如下:物料成本245.8元+制造成本15.53元=261.33元,在后文中讲解了ERP中的数据传递给MES后,MES作为下游数据接收方的使用逻辑,目的是降低运营成本,获得有竞争力的市场产品价格。
MES系统

MES是面向制造企业车间执行层的生产信息化管理系统。与ERP相比,二者各有分工,又相辅相成。从功能层面看,ERP无法对生产线设备做出实时响应,而MES可以做到毫秒级的实时响应,二者相得益彰。从信息交互的层面看,ERP往往是较封闭的系统,仅将信息单向传递给MES,而MES兼容并蓄,与设备层是双向通信。二者对接使用可以打通系统、数据之间的壁垒,提高效率。
MES的主要功能有很多,本文主要以ERP与MES垂直方向的结合应用为例进行研究,从订单转化、自动排产、物料拉动和工序防错四个方面进行介绍。
1.订单转化
供应链部门作为企业运营对外的重要窗口,负责接收来自客户的订单,然后转化为工厂内部的订单,内部订单往往涉及层面复杂,如预加工、最终装配加工等。在此,组成该型号仪表共有18个零件,其中8个是内部自制,即“自制半成品”,自制半成品的制造周期千差万别,需要依赖系统自动完成;剩余的外购品就需要提前将订单传递给供应商,提前备货。大部分汽车零部件企业都使用SAP系统,完成内部订单创建,订单完成后,可以自动推送至camLine,camLine接收订单后可以提前对人、机、料等资源进行准备和调度,确保生产计划的顺利进行。
2.自动排产
SAP系统具备自动排产模块,借助该模块,计划员只需要输入产品型号、数量及交货时间等关键信息,系统将自动确认物料库存信息和推荐各个生产线的具体排产计划。根据产品型号、数量和交付日期等订单要求,SAP自动推荐排产计划,人工确认后SAP将发出订单给camLine系统,camLine系统接收订单后,就可以授权设备严格按照订单开始生产。这样做的好处是不过量生产、不提前生产,做到精益生产所提倡的“刚刚好”。数量完成后,订单自动关闭。
除了自动排产外,同时具备计划管理功能,如查看、临时紧急订单插入等。
3.物料拉动——成品反冲
随着生产线各个工位消耗零部件,最终工位上源源不断地下线成品,物料流需要持续拉动式生产,那么如何在恰当的时间补充恰当型号、恰当数量的原材料就成为考验物料流设计的关键。
根据生产线成品下线工位的产出数据进行及时成品在线反冲(最快可做到5min/次的刷新频次),如图3左侧方框“Backflush成品反冲”所示,这样可以大幅缩短制程周期(A类原材料进入工厂到成品合格下线的时长),其他方面的潜在优势同样巨大,如减少在制品WIP的数量、快速交货及减少仓储规模等,图3中黑色虚线表示反冲数量与订单数量是此消彼长的关系。同时,工程变更导致的BOM变化与生产计划需要紧密配合,否则就存在错误使用零件的巨大风险。
图 3 SAP 与 camLine 系统逻辑关系
4.物料拉动——无纸化零件清单和自动叫料
笔者所在公司根据上文中讲述的原理开发了Replenishment项目:根据成品反冲数据自动拉动物料的补给。并在此基础上自主开发了新功能:无纸化零件清单和自动叫料。
传统生产车间物料配送的典型场景是物料员按照生产计划上的型号和数量,在生产线现场拿取对应的零件清单后,人工换算各个原材料箱数,之后是仓库领料、配送。零件清单是由工程师根据SAP中的BOM信息人工编辑而成的纸质文件。这样的模式有诸多问题:SAP系统数据与零件清单转化中易错,配送工作效率低,配送过程易错等。由于SAP中已经存储了BOM信息,SAP产生订单时同步将生效的BOM信息发送给了camLine,依靠这个电子数据可以开发出无纸化零件清单,配合在线成品反冲,可以实现自动叫料,车间内部微物流,如各个生产线的物料拉动、补给和配送就可以依赖该数据进行自动化运行。本项目取得了显著收益:生产线的配送频次由8h变为1.5h,持续精确流动;由于在线缓冲物料减少带来了生产线布局的大幅度缩小,减少到原来的48%;原材料库存降低了30%。
5.工序防错
为了实现产品的工序防错,如跳工站和重复上工站,依赖系统中的Routine数据,可以彻底解决该难题。
结语

汽车行业分工细致,主机厂和零部件行业协作水平较高,同时伴以深度的全球化分工协作,放眼整个工业领域首屈一指,对其他行业来讲有标杆性意义。在实现上述目标的过程中,ERP与MES的结合应用是核心所在,二者的互相匹配和协作可加速运营数据垂直方向的整合,快速实现数字化工厂和智慧工厂,同时对其他行业也具有启发意义。
文章来源: 汽车制造业
- 还没有人评论,欢迎说说您的想法!