基于数字双胞胎的智能制造系统的设计与应用
导 读
本文主要介绍了基于数字双胞胎的智能制造系统的组成、生产过程,并从设备、车间、企业、社会、应用等层面介绍了其设计,并提出了对数控系统的新要求,基于云系统的维护,可视化管理等。
作者:韩鸿鸾
基于数字双胞胎的智能制造系统的组成与工作过程
1.基于数字双胞胎的智能制造系统的组成
数字双胞胎是物理产品在虚拟世界的镜像,如图1所示。数字双胞胎是物理资产的虚拟镜像,借助传感器采集数据反映机器的实时工况、状态和位置,通过模型优化后,返回现实世界以提高机器性能。数字双胞胎也可用于监控、诊断和预测,数字模型借助物理对象的数据积累,分析机器的健康衰退程度,提出预测性维修方案。
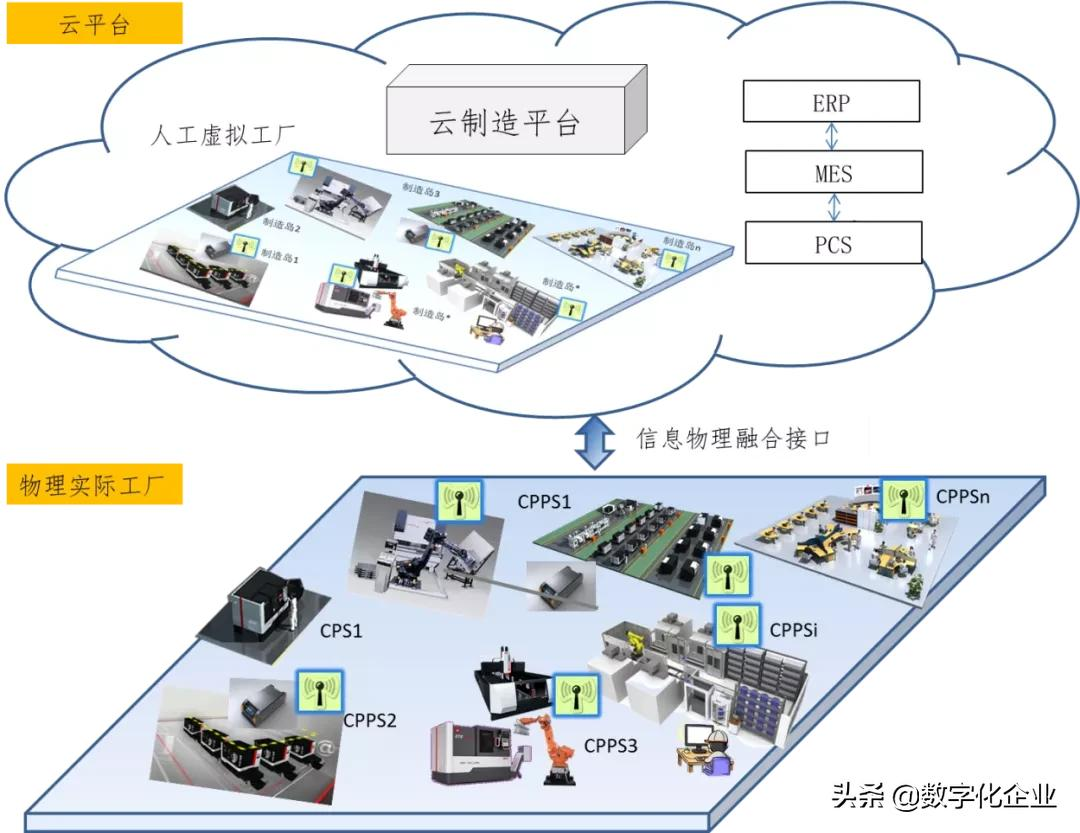
图1基于数字双胞胎智能制造
智能制造领域应用的数字化双胞胎技术与传统制造相比如图2所示。其核心技术为信息物理融合生产系统(CyberPhysical Production System-CPPS),如图3所示,信息物理融合生产系统(Cyber Physical Production System-CPPS)是信息物理融合系统(CPS)在生产领域的应用,是一种多维度的智能技术体系。信息物理融合生产系统以大数据、网络和云计算为依托,通过智能感知、分析、预测、优化、协同等技术手段,使计算、通信和控制三者有机融合与协作。将所获取的信息与对象的物理性能表征相结合,形成虚拟空间与实体空间深度融合、实时交互、互相耦合、及时更新,在网络空间中构建实体的虚拟镜像。通过自感知、自记忆、自认知、自决策、自重构的运算和分析,实现生产系统的数字化、智能化和网络化。
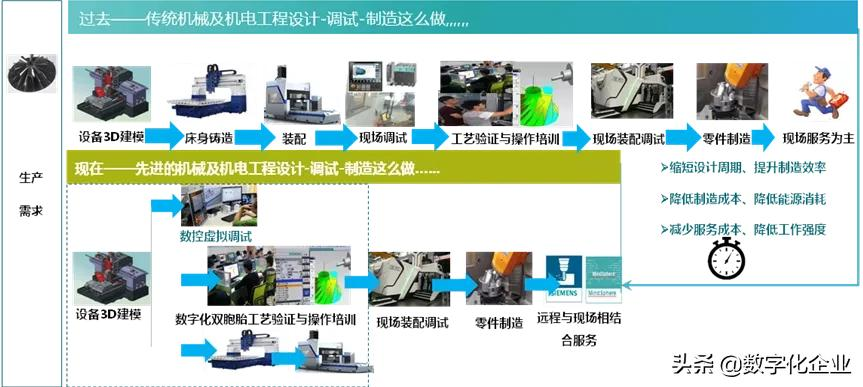
图2应用数字化双胞胎技术的智能制造与传统制造比较
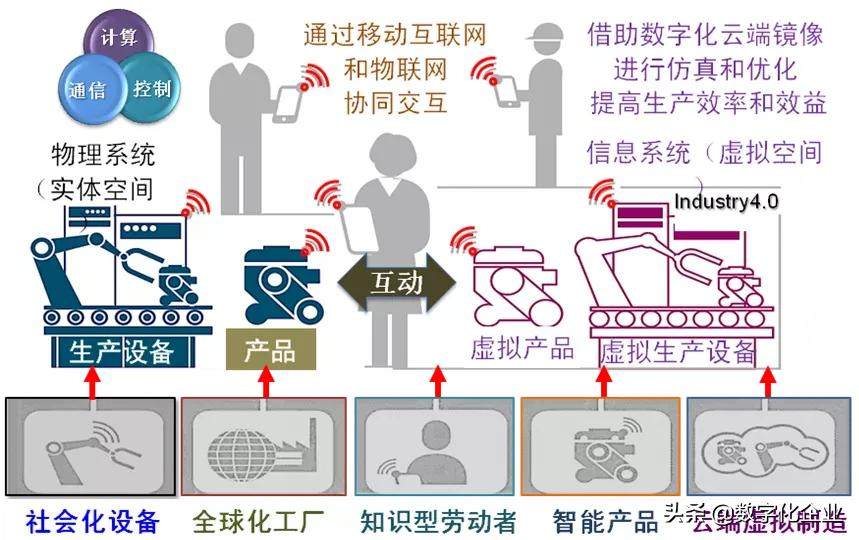
图3 核心技术
2.基于数字双胞胎的智能制造系统的工作过程步骤
第一步:数据的采集和处理,如图4所示。
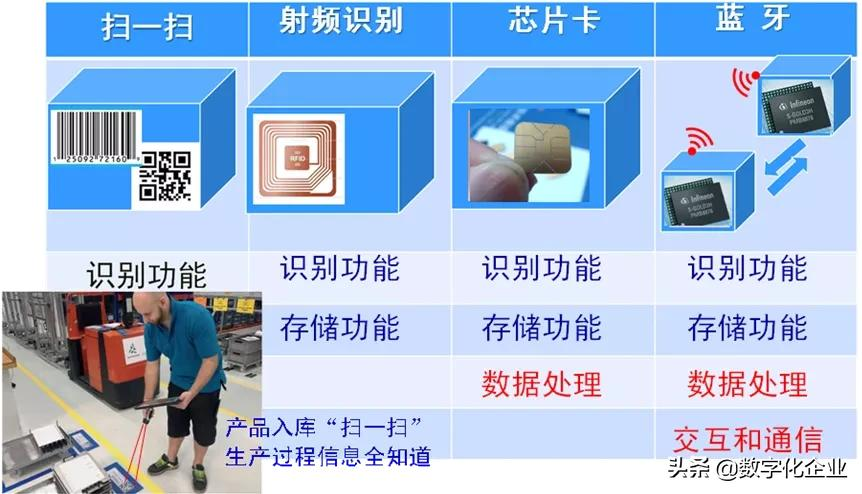
图4 数据采集
第二步:人机与机机通信
如图5所示,刀柄上有芯片,可记录刀具和刀片的规格、尺寸,刀具预调数据,推荐切削用量,将信息发送给机床数控系统。加工时,芯片记录切削参数和切削时间;还有多少剩余寿命,还可加工多少个零件,发送给操作者和有关部门。
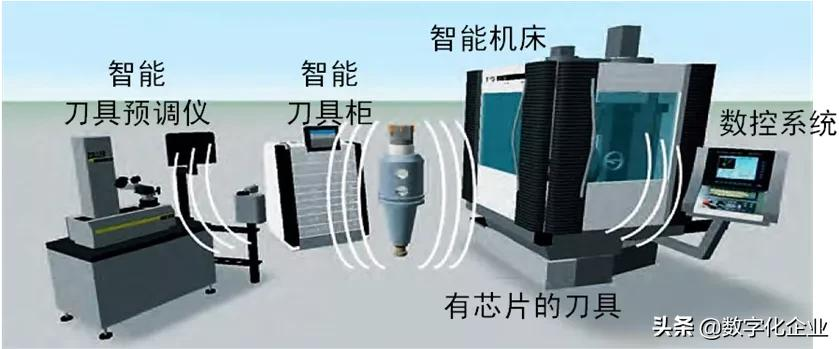
图5 人机与机机通信
第三步:如图6所示,从数据、信息到决策
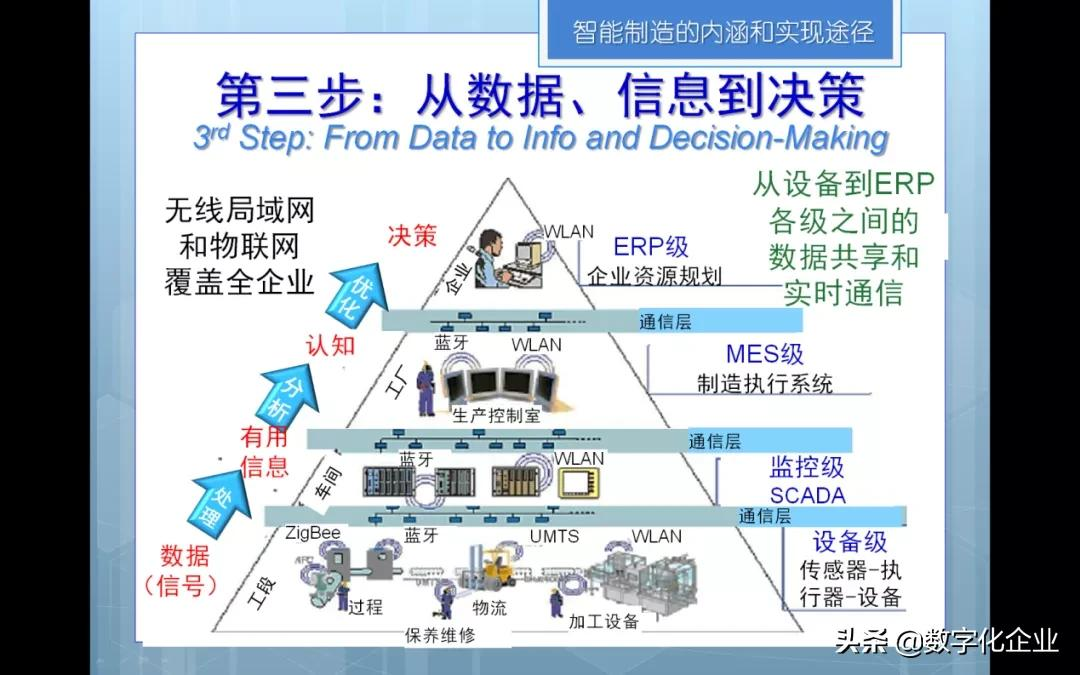
图6 物联网
第四步:迈向预测型智能制造
智能制造的困扰是设备和装置的失效,随着时间推移,设备会磨损,性能会衰退,最终导致故障和停机。
预测型智能制造通过掌握设备实际的状态,不是在故障发生后去抢修,或过早地将可继续用的部件进行不必要更换,而是采用计划性维修,从而降低维修费用和生产成本。知道设备什么时候可能失效,就能够合理地安排维修计划,实现“准时”维修,最大限度地提高设备的可用性和延长其正常运行时间,提升工厂运营效率。将设备衰退模式和实时状态评估与加工过程控制结合起来,实现在设备或系统性能随时间变化的情况下,保证产品质量的稳定,迈向“无忧虑”智能制造。预测型智能制造的层次和架构如图7所示,预测型智能制造的信息物理模型(Cyber-PhysicalModel for Enhanced Predictive)如图8所示,大数据分析是预测型制造的重要手段。
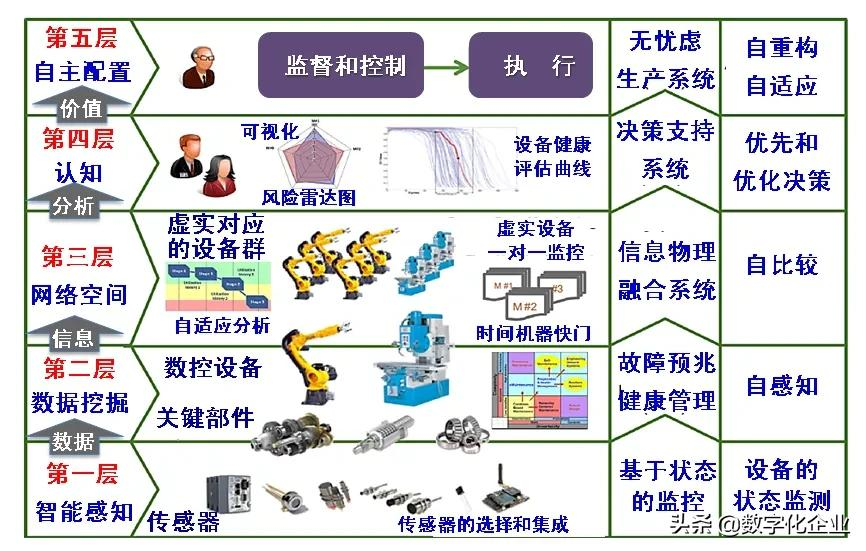
图7 预测型智能制造的层次和架构
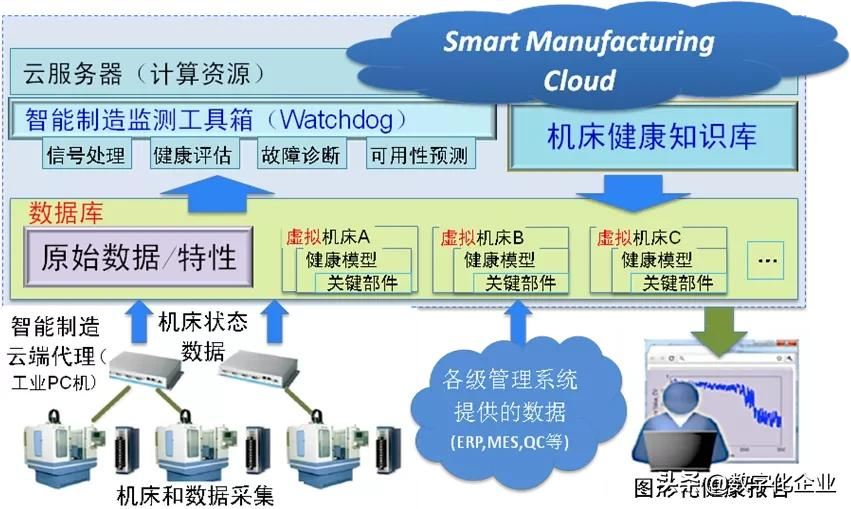
图8 预测型智能制造的信息物理模型
基于数字双胞胎的智能制造系统的设计
1.设备层面
(1)系统的要求
由制造过程透明可知使智能机床不再是传统的机械设备,而变成了一台智能终端,它不仅可以加工零件,同时能够产生服务于管理、财务、生产、销售的实时数据,从而实现设备、生产计划、设计、制造、供应链、人力、财务、销售、库存等一系列生产和管理环节的资源整合与信息互联,并为上述过程提供精准的数据依据,成为新工业革命的基础。
数控系统采用的G、M代码(ISO 6983)已不能适应现代化生产和技术发展的需要。STEP-NC将产品数据转换标准STEP扩展至CNC领域,重新定义了CAD/CAM与CNC之间的接口,如图9所示。它要求数控系统直接使用符合STEP标准的CAD三维产品数据模型(包括几何数据、设计和制造特征),加上工艺的信息和刀具信息,直接产生加工程序来控制机床。要求具有更顺畅的操作、更高的生产效率、强大的工厂管理支持、更好的客户化功能扩展、多通信协议支持。可采用云数控系统,如图10所示。
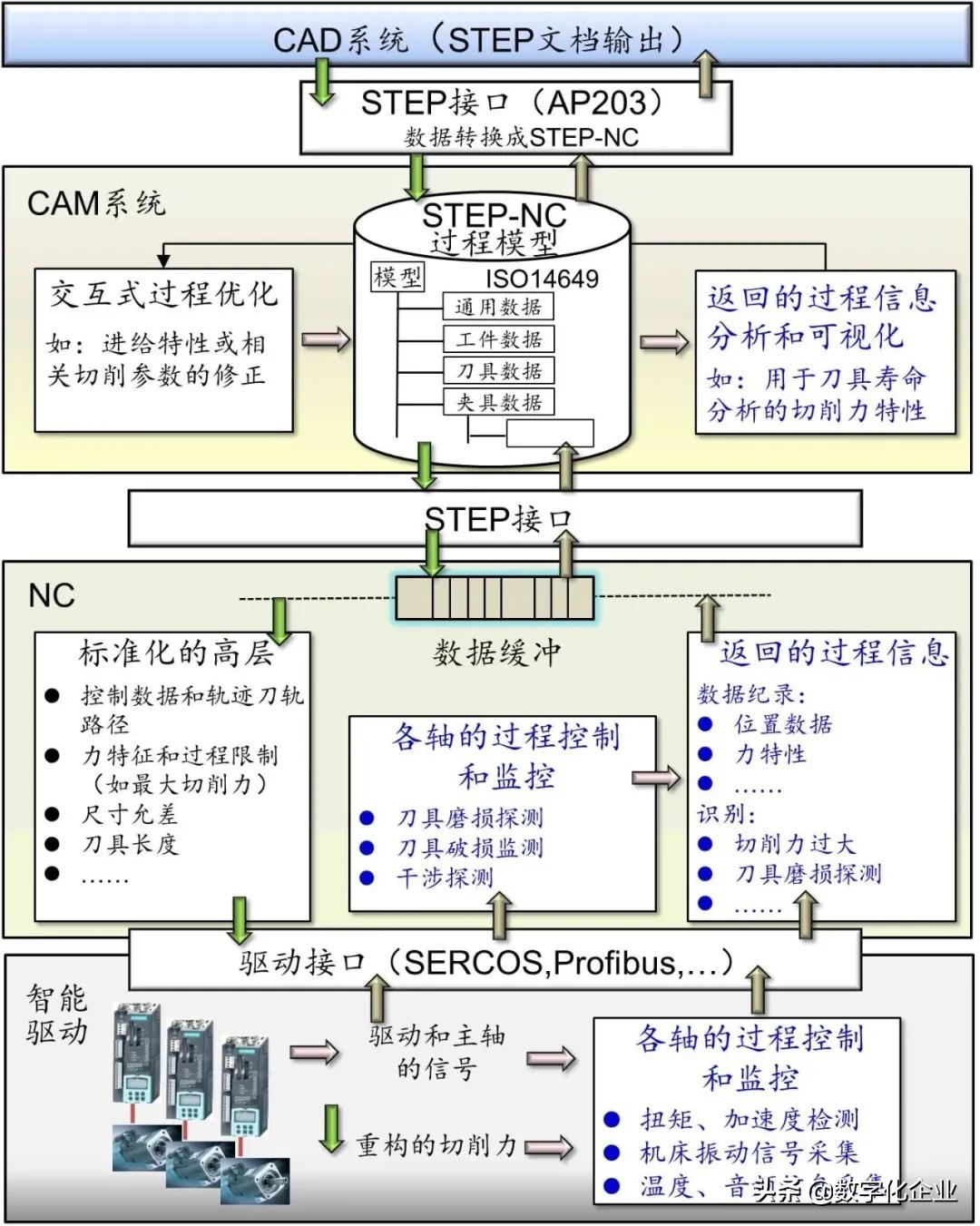
图9 STEP扩展至CNC领域
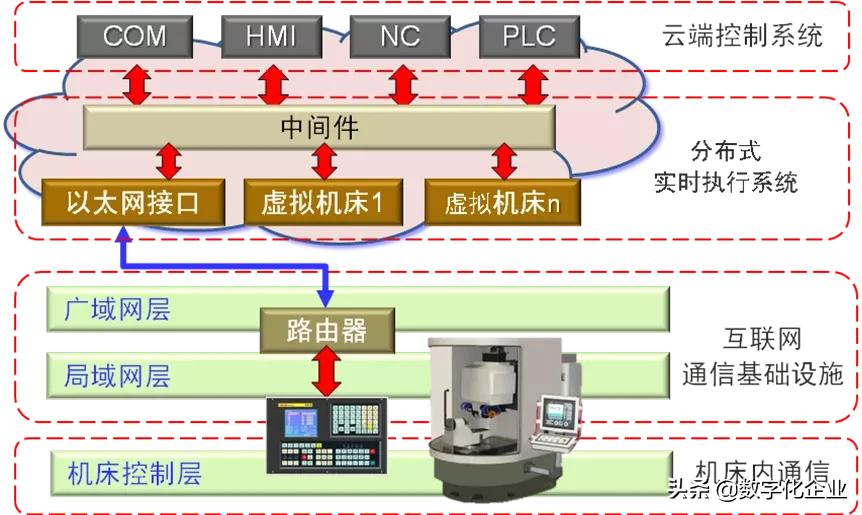
图10 云数控系统
(2)对设备提出了如下要求
智能机械加工工厂对机床的要求是能够接入互联网络,能够实时向网络提供自身的相关信息(如:运行状态、工作内容、工艺数据、工作进度等),能够从网络接受所需的各种数据(如:加工程序、生产计划、工艺数据、生产准备信息等),通过智能化的功能最大程度减少生产准备工作内容,具有一定的自适应功能,具备自我诊断的能力。
1)机床装备高端化主要包括高速高精加工,加工过程自动化(机器人取代操作工人),车间物流自动化(AGV自动配送混流物料),产品检测自动化(生产现场非接触光学自动检测、系统采集数据,及时反馈结果)。将数控机床接入企业信息化网络,连接CAD/CAM、MES、ERP、PPS以及PDM等信息化软件,如图11所示。
图11 智能数控机床
2)工艺数字化(图12)
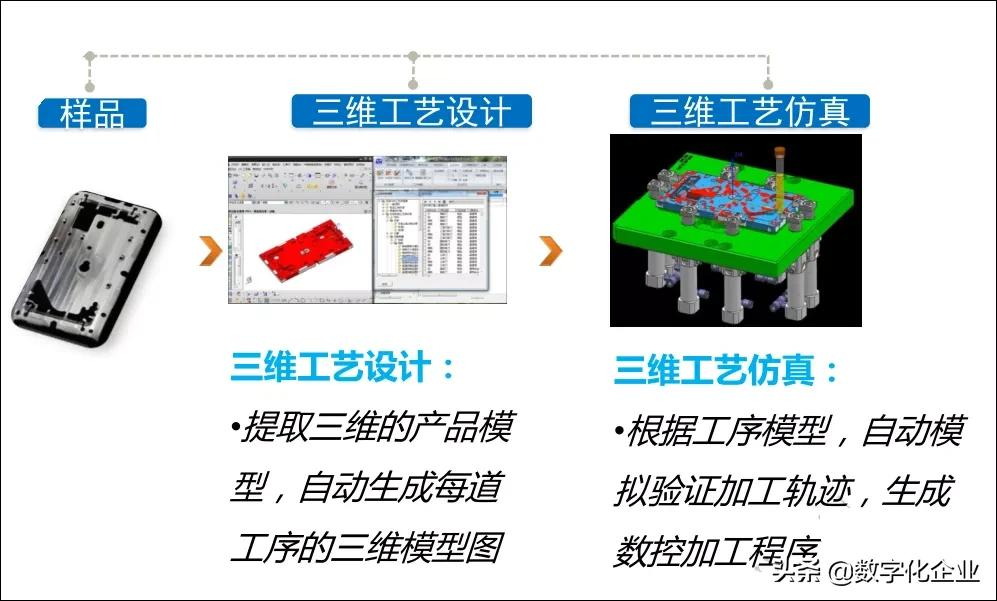
图12 工艺数字化
3)生产柔性化(图13)
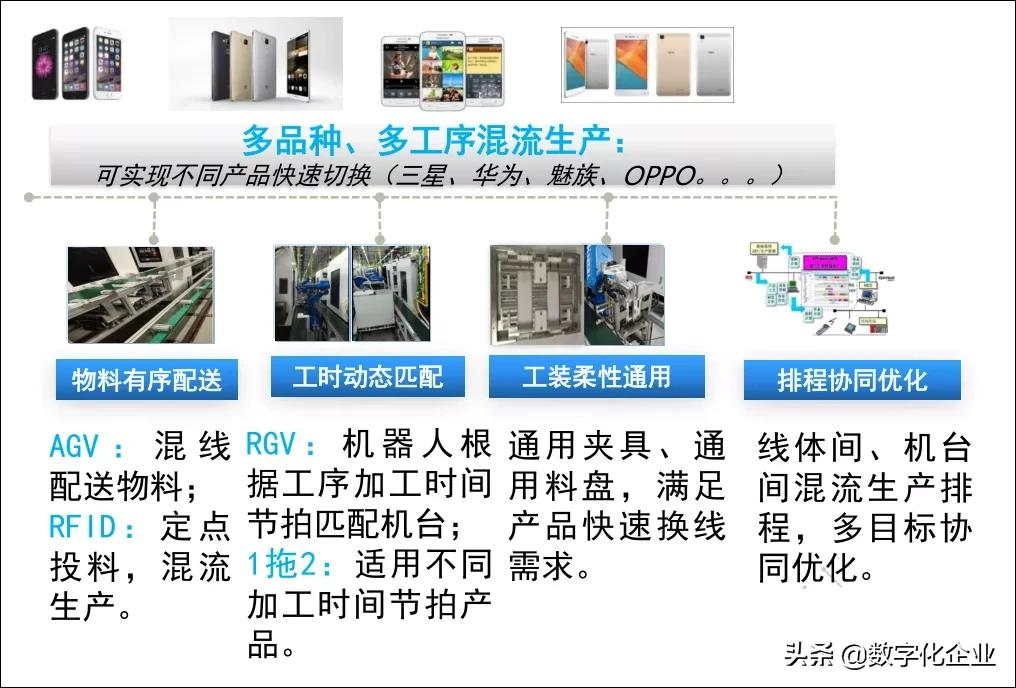
图13 生产柔性化
4)过程可视化
如图14所示,实时上传:数控机床、 机器人 、 RFID料盘 、 AGV 、 RGV 等各种设备数据, 物料数据及生产状态数据;指令下发:生产与物料指令 、工艺数据、 质检标准等下发至设备。增强现实技术等先进技术在智能制造中得到应用,如图15所示。
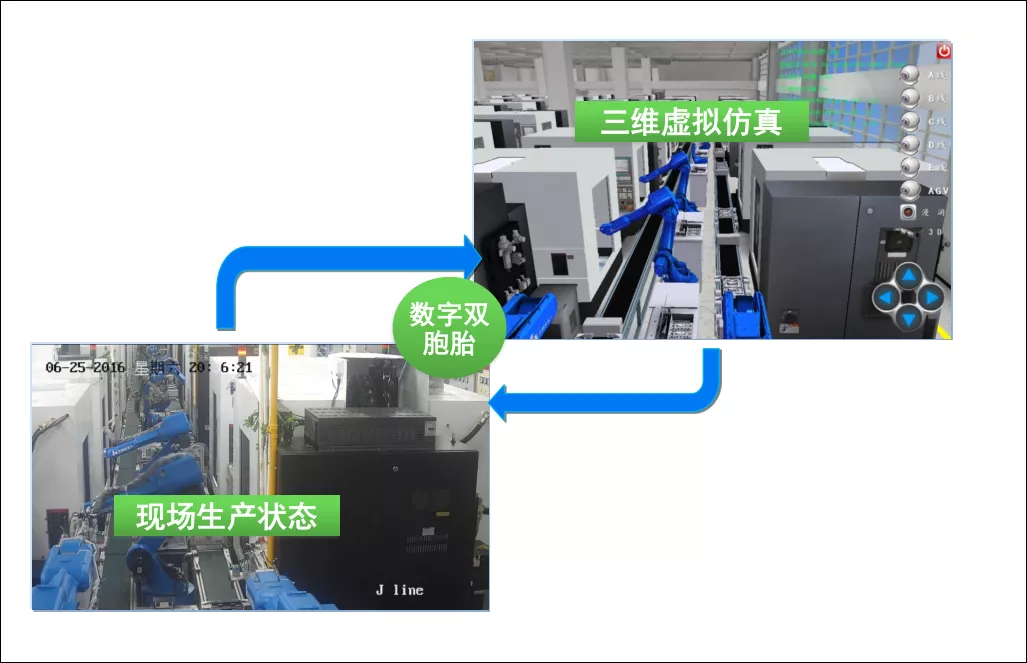
图14 过程可视化
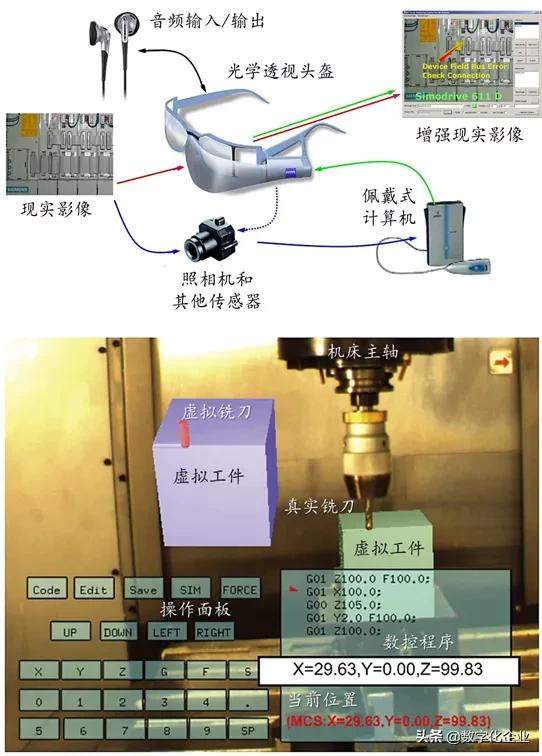
图15 增强现实技术在智能制造中得到应用
5)信息集成化
要求有虚拟服务器与海量信息存储处理能力,车间信息集成网络,具有一网到底实现所有信息采集与集成功能。
6)决策自主化
具有企业管理自决策,生产管控自组织,制造过程自执行,设备状况自检测等。
7)数控装备具有智能化,如图16所示。
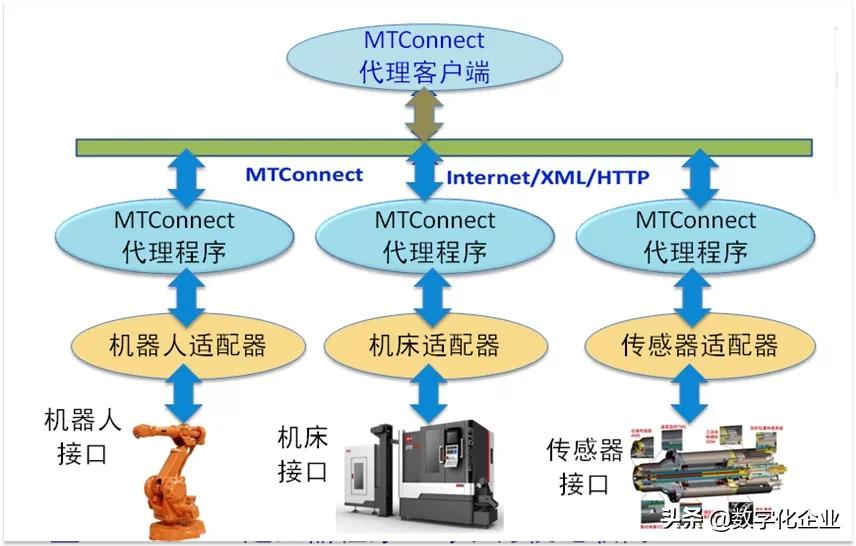
图16 数控装备具有智能化
8)自主机器人
如图17所示,自主机器人应具有机器人自主导航(Robot navigating autonomously)、按生产需要调整机器人路径(Robot path adjusted to production needs)、机器人路径不受轨道限制 (Robot path not limitedby rails)、生产流程易于再规划(Easyre-planning of production flow)、为机床服务(Machinetool world),比如将刀具送到机床上(Bringcutting tools to the machine)、将毛坯送到机床上(Bringraw pieces to the machine)。
图17自主机器人
2.车间层面
对于车间层面来说,基于云系统的信息平台能提供贴身的管家式服务,无论何时何地,无需冗长的报告,只需点击终端,所有信息尽在掌握,如图18所示。
如图19所示,基于云系统的维护平台提供远程故障诊断服务,自动发送故障提醒短信, 支持基于地理位置的故障报修,专家远程在线检测,轻松完成系统诊断、升级、备份、恢复。重点是以下工作。
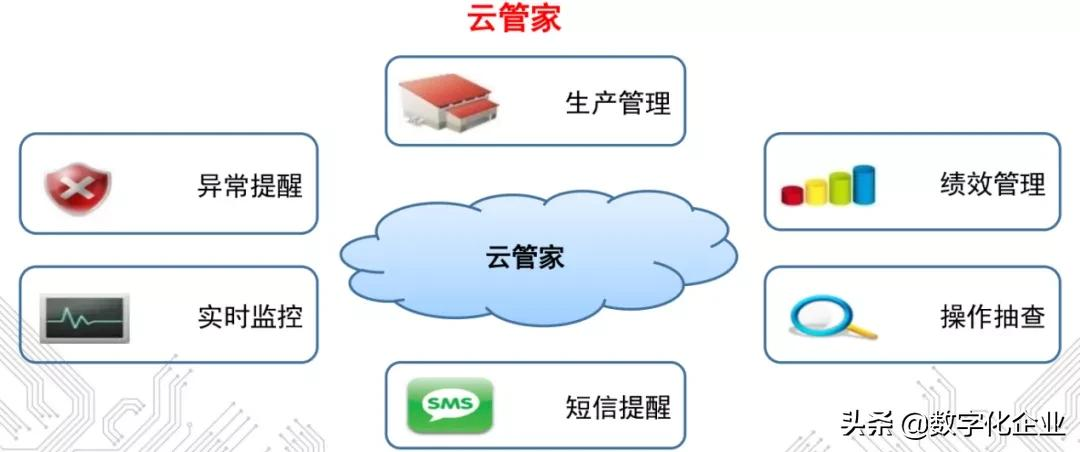
图18 云管家
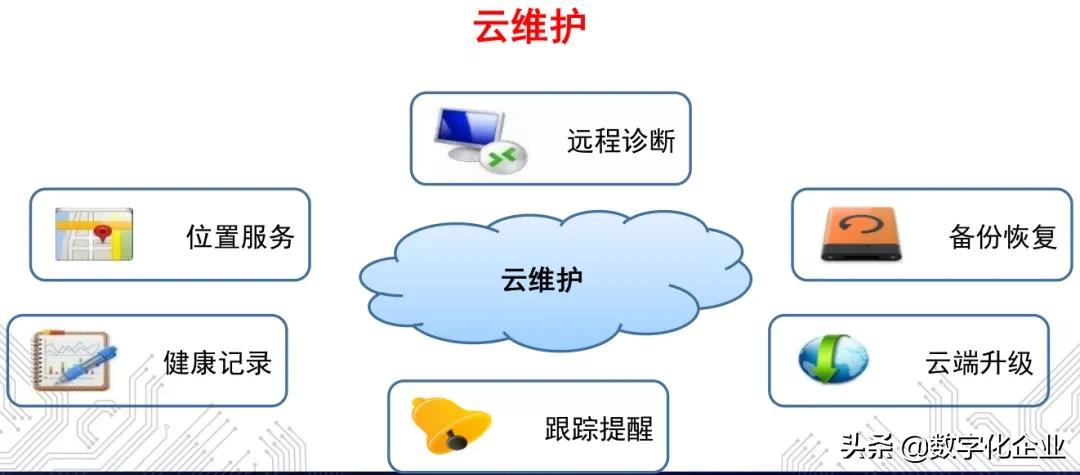
图19 云维护
基于云端强大的服务器资源和专业软件的增值服务,在编程、工艺、优化的专有功能,可以将“特色应用” 有偿共享给所有其他用户,使数控系统更智能、更专业。如图20所示。
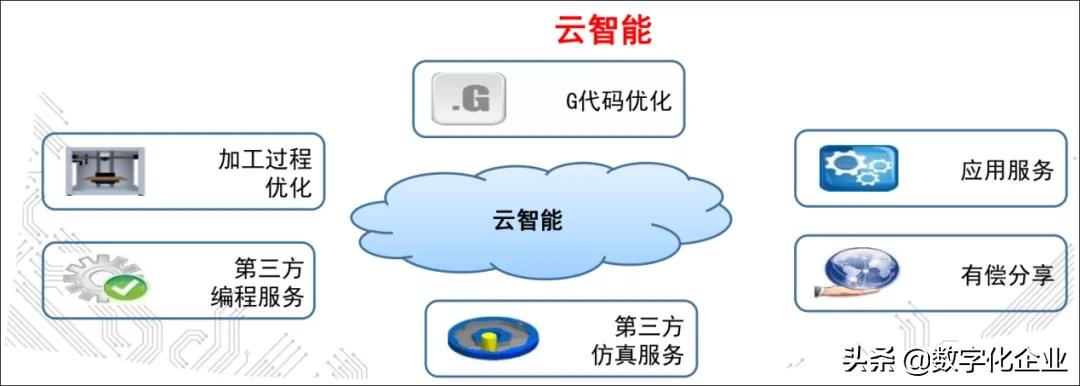
图20 云智能
1)针对为员工提供人性化工作条件的设计标准,如图21所示。
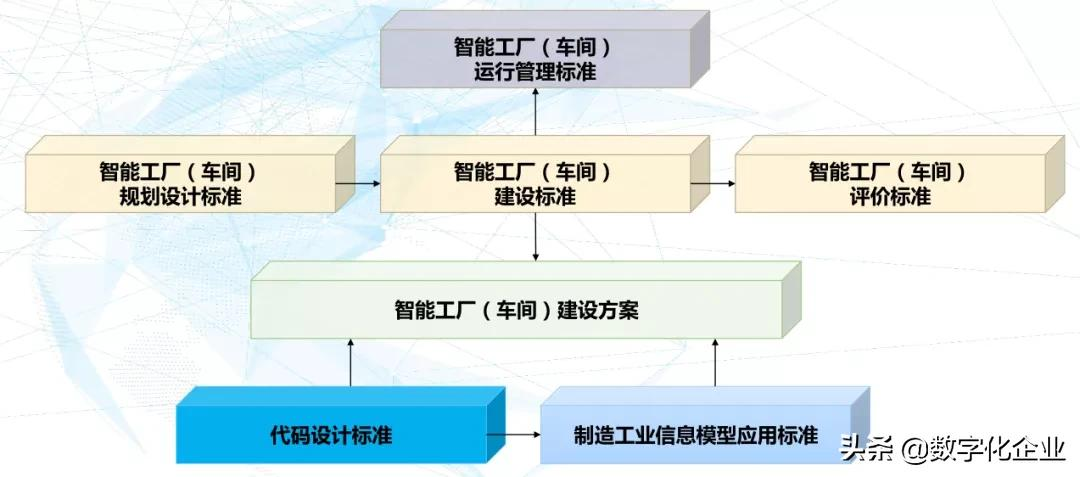
图21 标准制定
2)云平台的建立
利用控制信息、传感信息、网络信息,实现从数控设备的运行、加工、操作和编程等环节中,替代人脑,完成工作。包括:智能管理、智能调试、智能补偿、智能加工、健康保障、网络销售平台等,如图22所示。
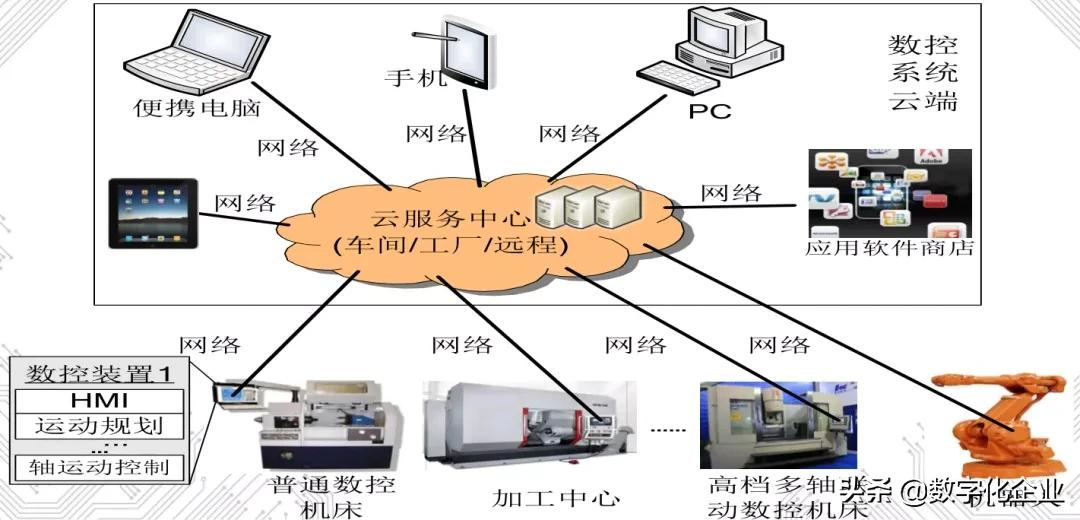
图22 云平台的建立
3)云数控服务平台
如图23所示,利用远程监控管理手机APP智能管理、远程监控车间。
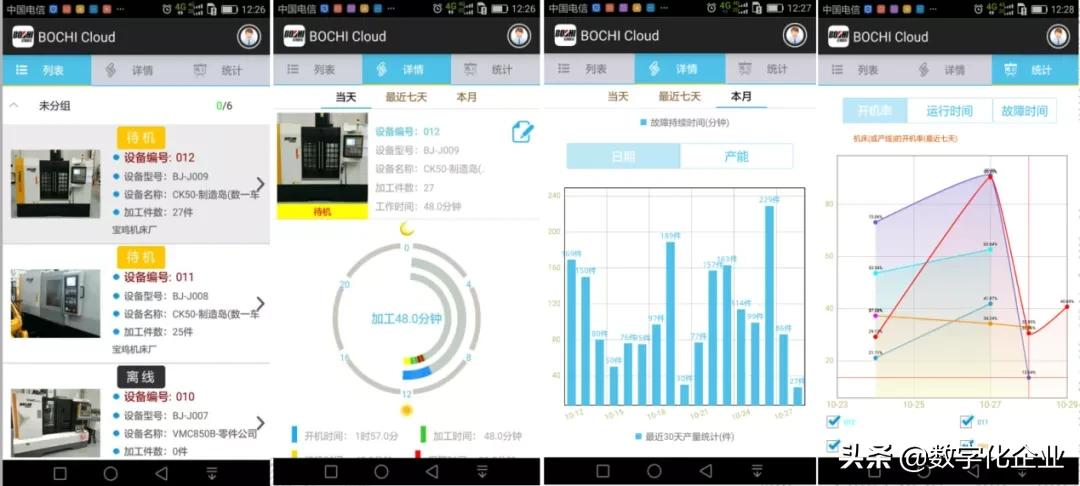
图23云数控服务平台
3.企业层面
(1)组成
智能制造工厂是基于信息物理融合 (CPS)的智能系统,采用更标准化、智能化的媒介和载体结构减低复杂性;实现实时柔性制造和生产过程智能化。基于实时生产仿真模型和集成化制造管理系统,实现人工智能化动态生产决策;基于知识和虚拟仿真系统,推理全面满足客户化需求的最佳方案,颠覆传统“厂家生产什么,客户只能买什么”模式。为客户提供价格更低,更开放市场和更多样化产品;跨企业价值链业务集成,构建端到端的价值流,形成新的业务模式。企业的数据平台如图24所示,智能工厂的特征如图25所示,效益如图26所示,组成与建厂步骤见图27与图28。
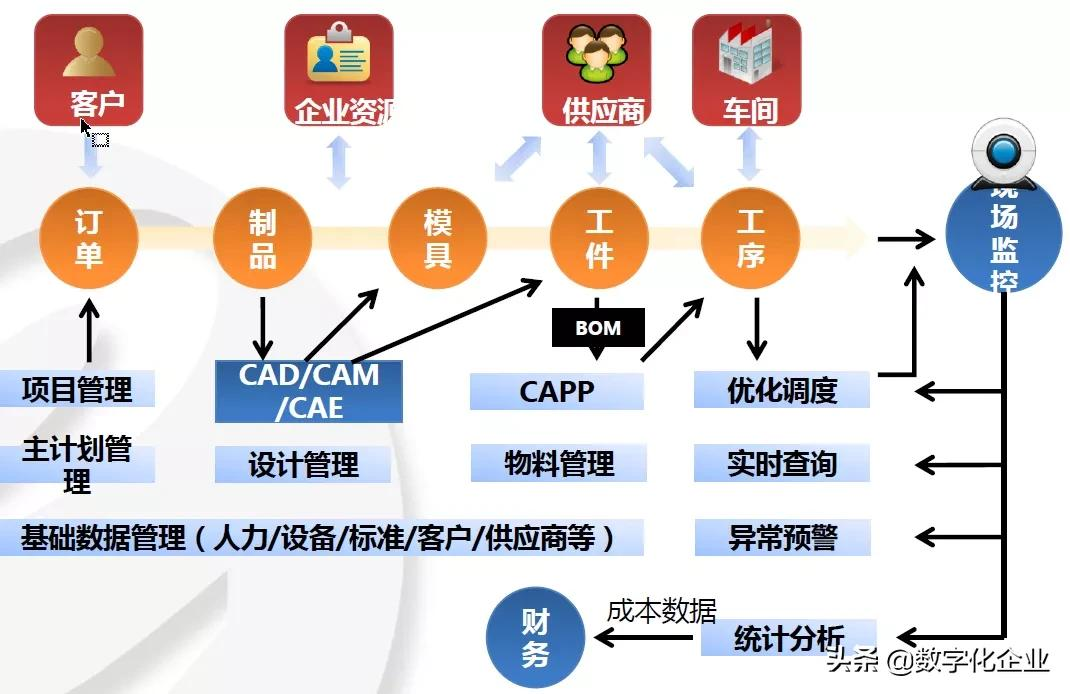
图24 企业的数据平台
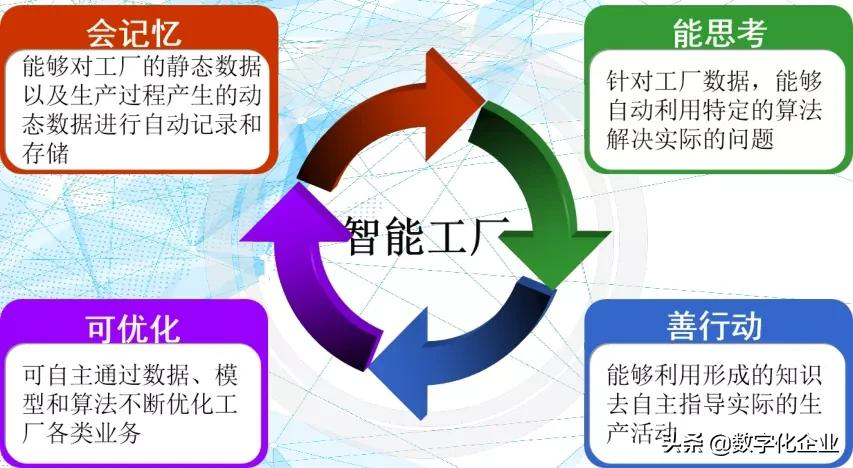
图25 特征
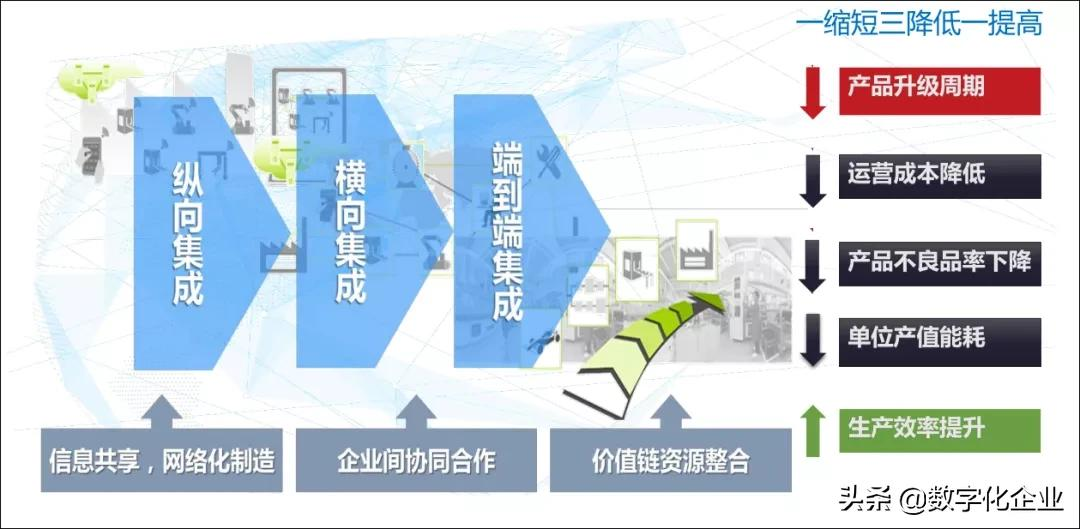
图26 效益
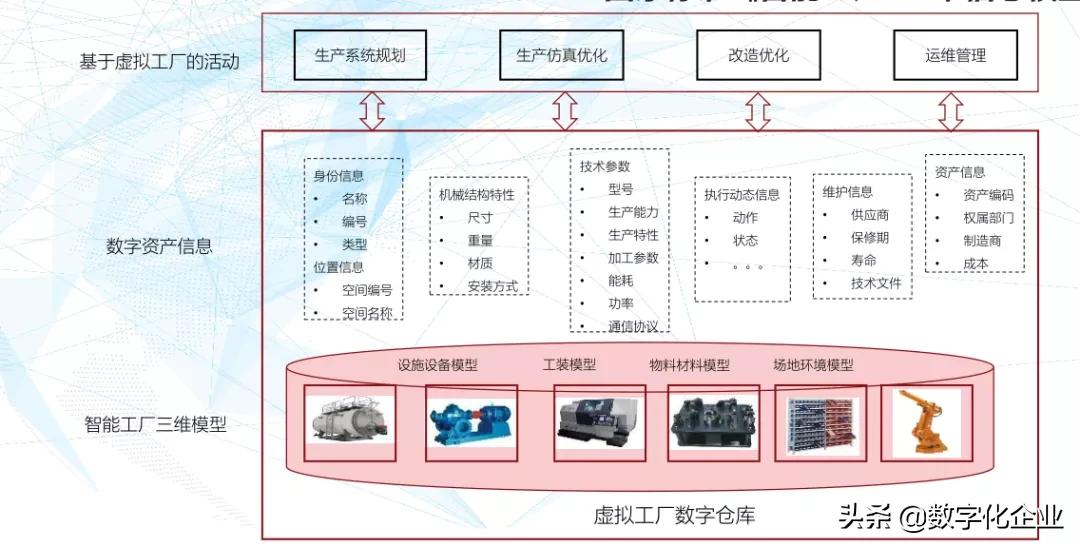
图27 组成
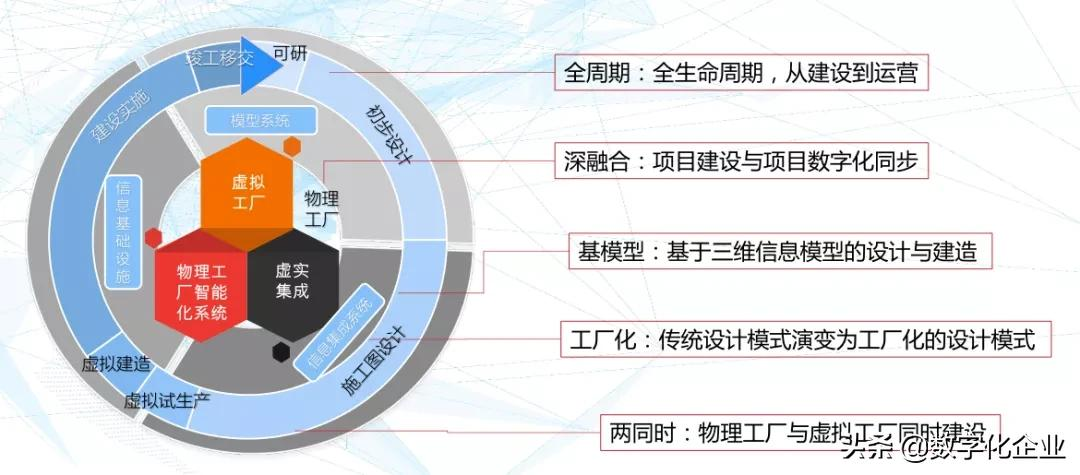
图28 步骤
(2)特征
1)工厂大数据中心
智能工厂的 基本功能、设计要求、 设计模型类标准等总体规划标准;达成智能工厂规划设计要求所需的 仿真分析、协同设计 和 建设实施标准等实施指南标准;基于智能工厂的 工艺流程及布局模型、 生产过程模型和组织模型 等系统建模标准。如图29所示,智能制造的核心是数字化、网络化、智能化。
一是数字化:对工厂中数控机床、机器人、工具、刀具、人等全部制造资源的实时数据采集,实现智能工厂的数字化;
二是网络化:通过对实时数据的网络化传输,在大数据中心中汇聚、储存和管理,建立了智能工厂的“数字双胞胎”;
三是智能化:在描述智能工厂“数字双胞胎”的大数据中心之上,使用了PLM、CAPP、MES、ERP等智能工厂信息化管理软件,以及基于大数据的工艺优化、断刀检测、健康保障等智能化软件模块,提高生产效率、生产质量,实现了智能化。
形成形象交互的3D虚拟车间,如图30所示。3D可视化支持CATIA、PRO/E、UG等多种数据文件无需转换的直接浏览,实现3D图形、工艺直接下发到现场,实现了生产过程的无纸化生产管理,如图31所示。
图29 工厂大数据中心
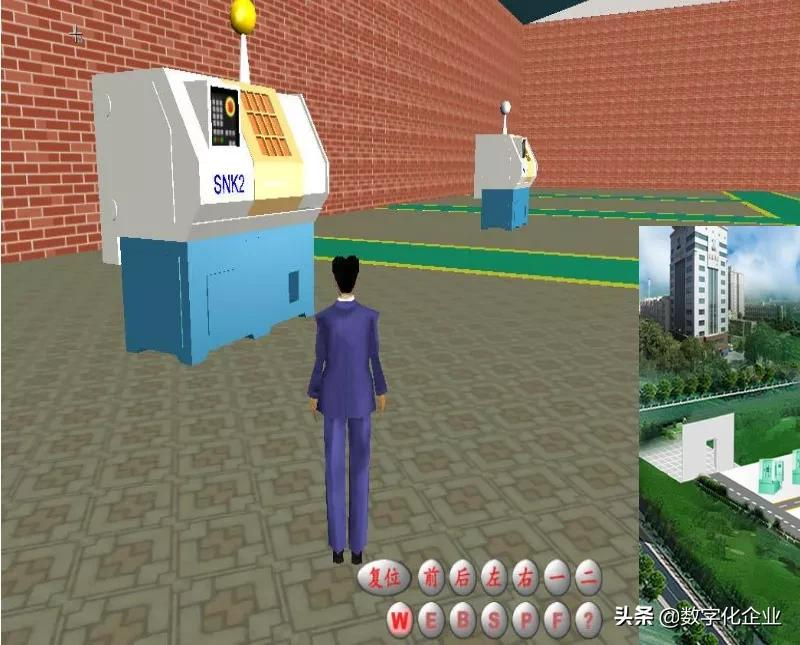
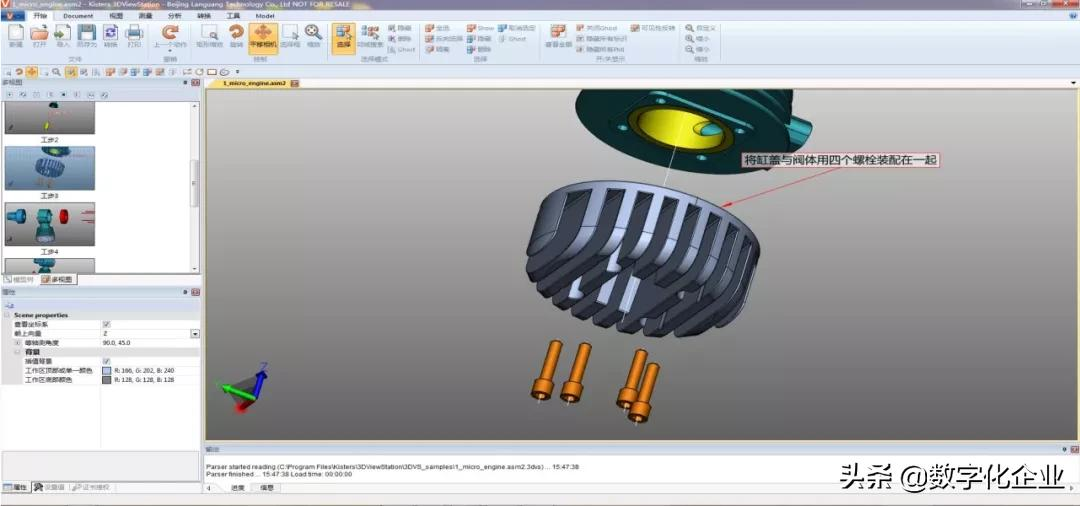
图31 无纸化生产管理
2)智能制造时代的经营战略
随着智能制造的推进,我们的竞争战略与制造模式将会发生很大的变化,需要向定制化(消费端就是个性化)、聚焦化、协作化、全球化的“新四化”方向发展。
3)六维智能工厂理论(图32)
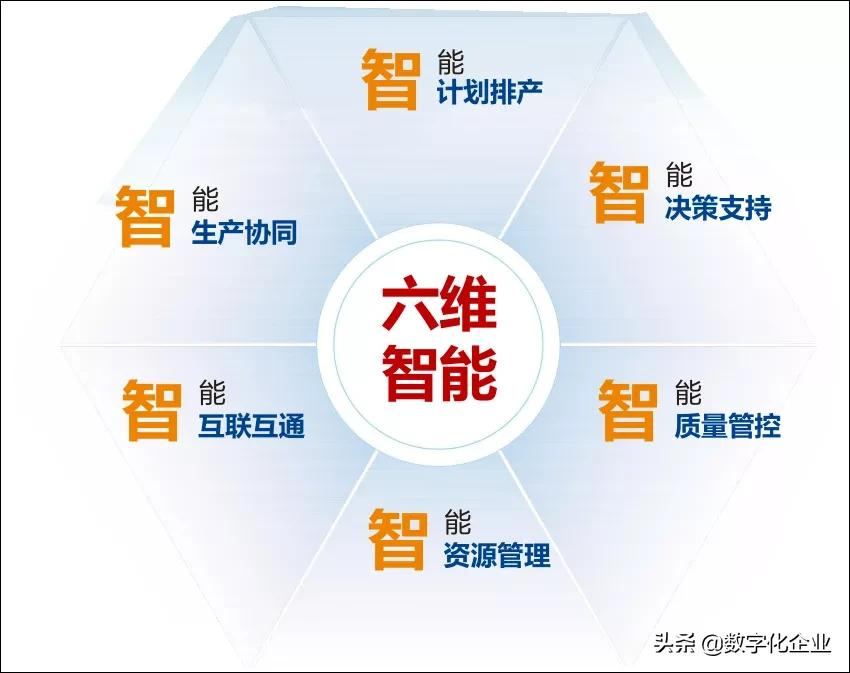
图32 六维智能工厂理论
4)平台化与智能化的MES系统(图33)
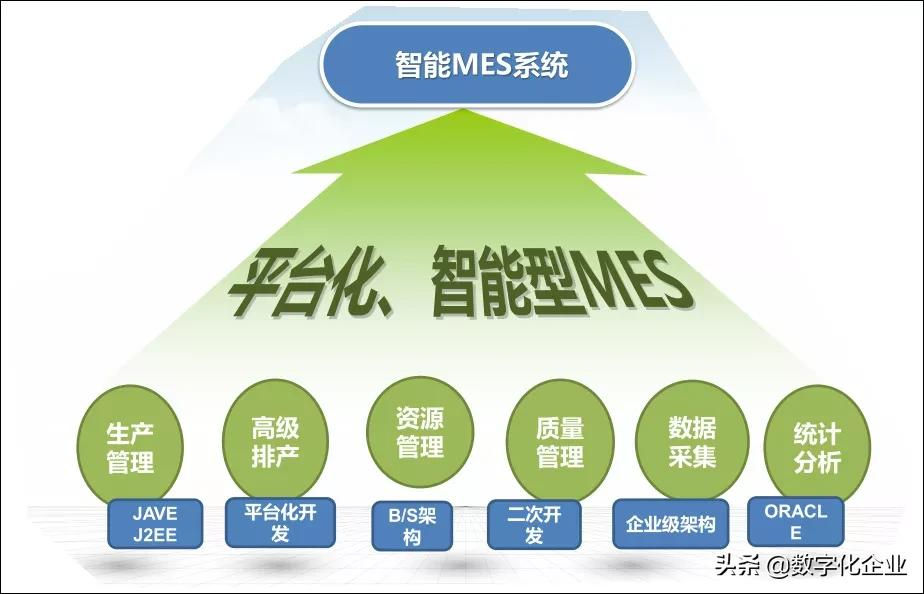
图33 智能化的MES系统
5)智能化的生产资源管理,优化库存,减少浪费,如图34所示。
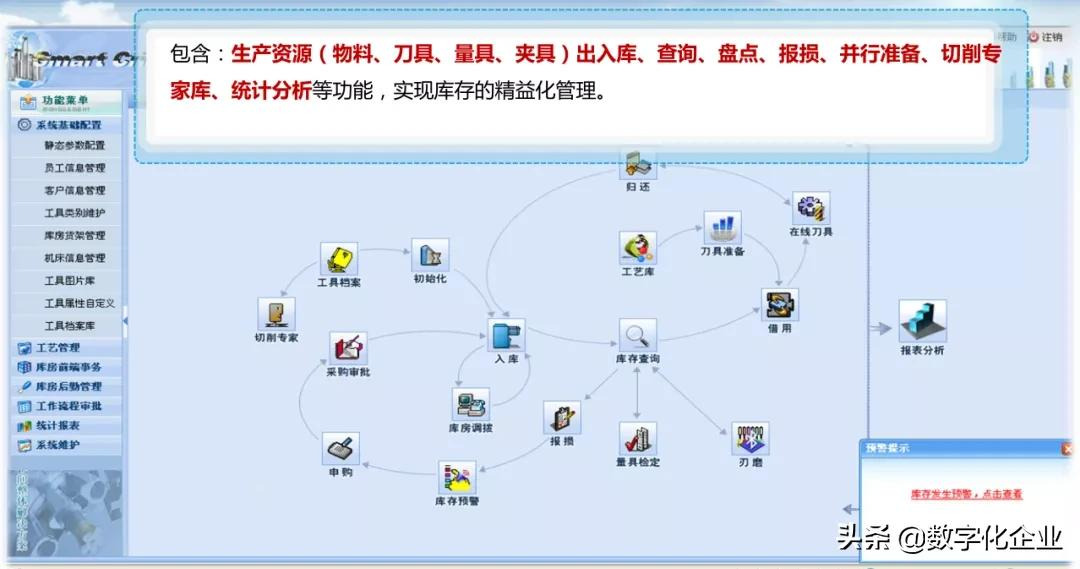
图34 生产资源管理
6)质量管控智能,生产工艺参数的实时监测、动态预警通过设置设备加工过程中相关工艺参数的技术指标(范围限值),对加工过程进行实时的、动态的、严格的工艺控制。结合企业的产品二维码信息,通过每个工件的唯一标识,在系统内部可以查询到,生产该产品时所采用的工艺参数及机床状态等信息,便于质量的追溯,如图35所示。
产品的质量取决于生产过程对工艺的严格管控。对工序过程的主要工艺参数与完工后的产品合格率进行综合分析,为技术人员进行工艺改进提供科学、客观的参考数据,如图36所示。
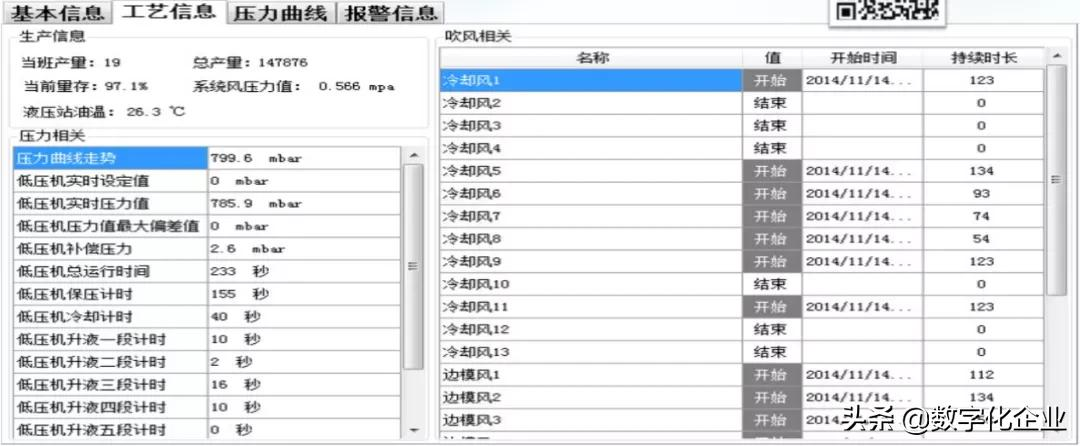
图35 工艺参数及机床状态等信息
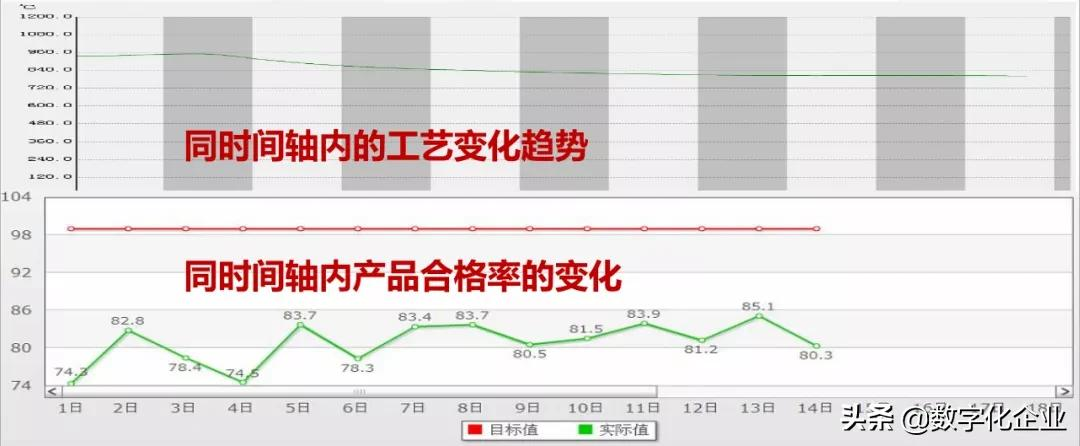
图36 变化趋势
7)智能化的决策支持目视化管理,提供各种直观的统计、分析报表,为相关人员决策提供帮助,包括计划制订情况、计划执行情况、质量情况、库存情况等,如图37所示。
实现用户在手机、IPAD等移动设备上对现场生产情况、设备运行情况、质量情况的数据浏览、异常处理,如图38所示。
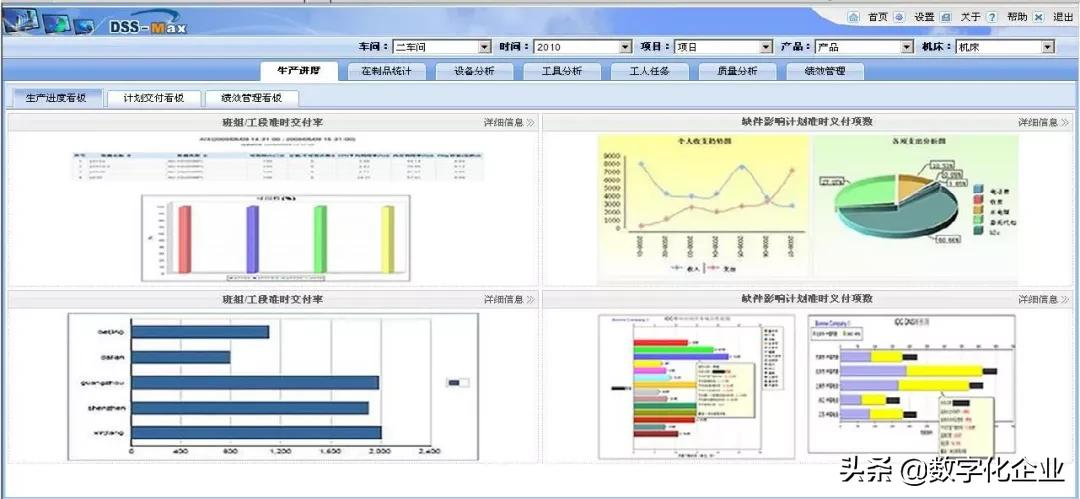
图37 智能化的决策
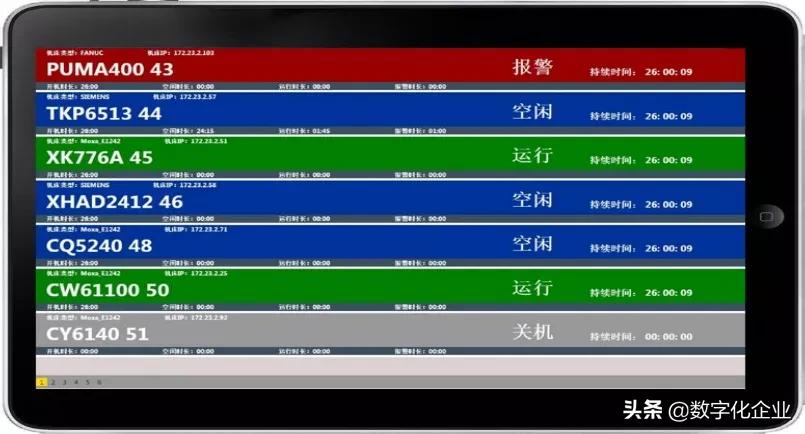
图38 移动设备上对现场生产情浏览
4.社会层面
智能制造工厂不仅是自动化,而是在数字化基础上的资源、技术、信息、组织和人文的全面集成。传统工厂的不同点首先在于生产流程的可视化和管理的透明度,看得见、易理解沟通,才能高效率、高质量。工厂的运维是动态的,未来工厂的“健康”状态是可预测和有预案的,有备无患。工厂是智能化的,具有自主管理和自优化的能力,能够适应客户需求和外界环境的变化,如图39所示。
互联共生不仅体现在网络连接,更重要是相互依存的共享业务关系。互联共生工厂需要工业互联网平台支持,以连接各种形式的服务提供者。生产不是孤立的与城市环境、供应链和电网相互配合,才能提高资源利用效率,发挥共生效应,如图40所示,其软件结构如图41所示。
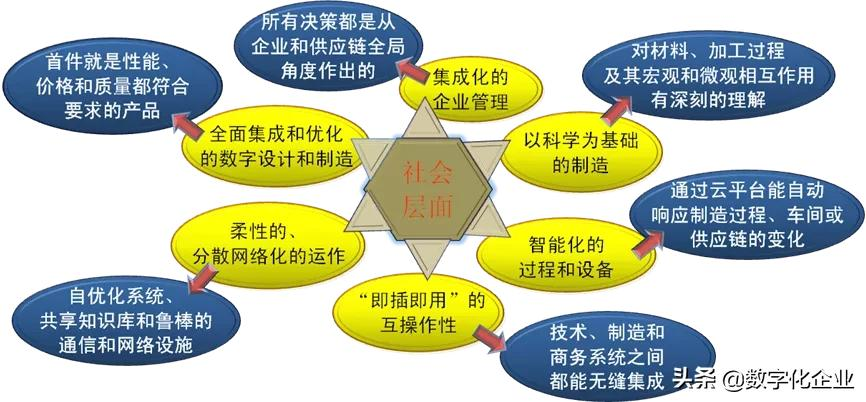
图39 社会层面
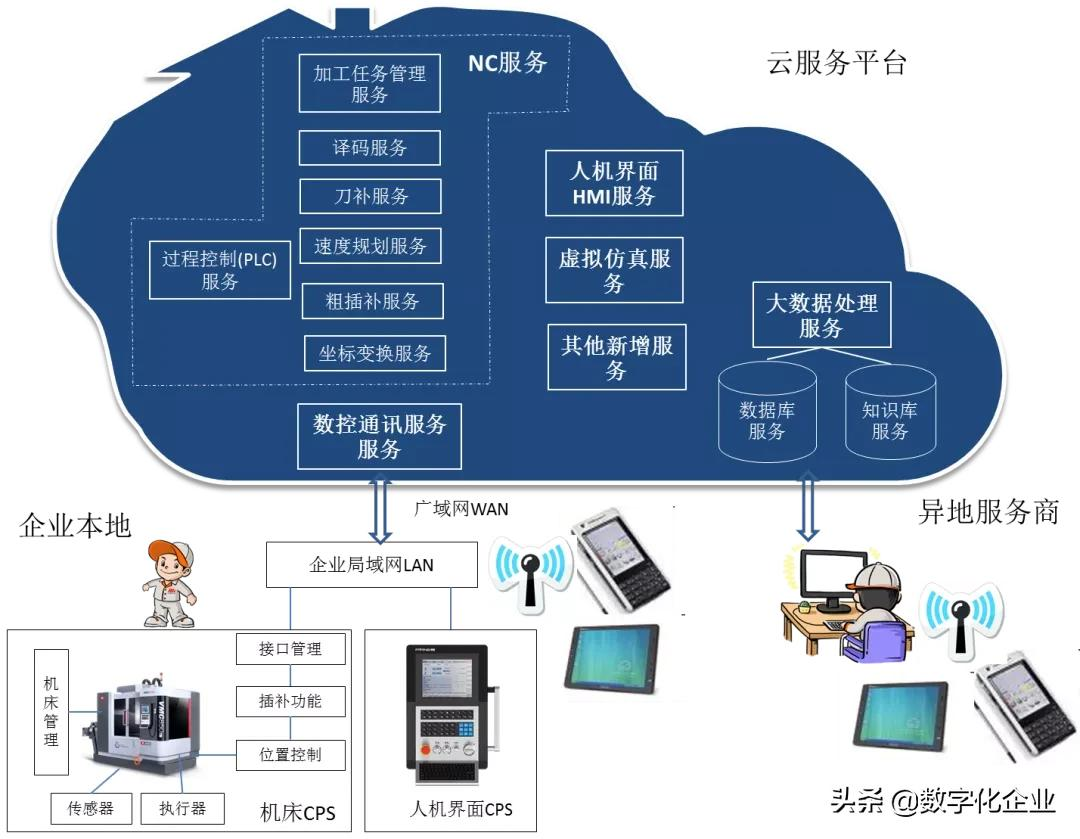
图40 互联共生
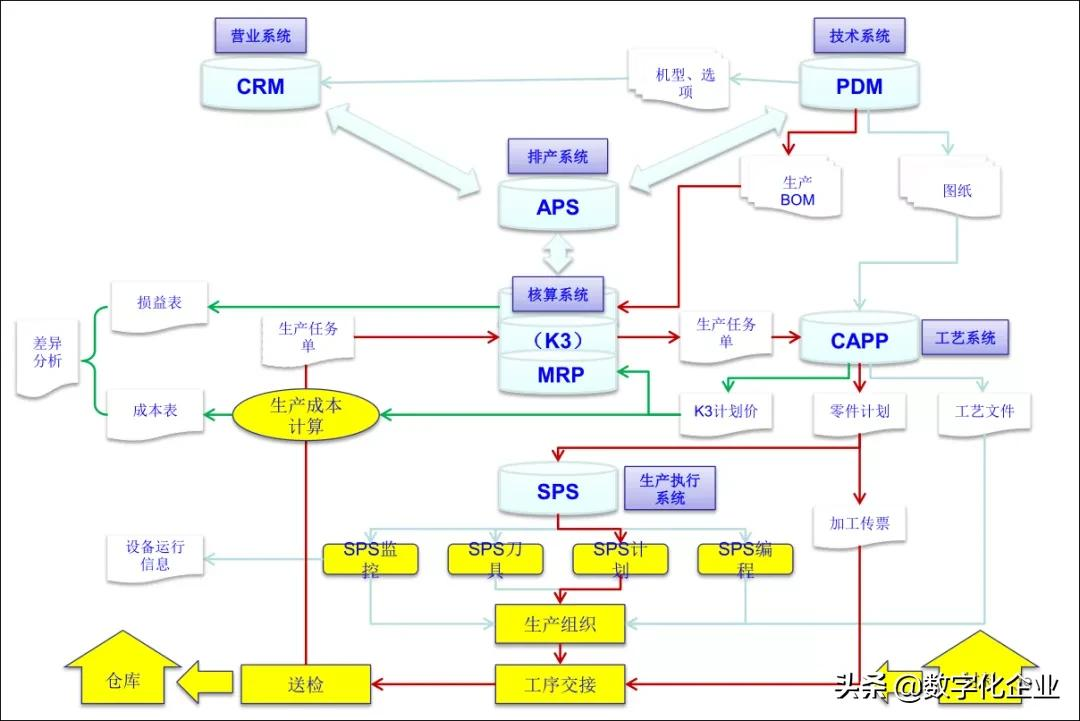
图41 软件结构
5.用户层面
(1)应用过程
1)创建 / 准备任务单(图42)
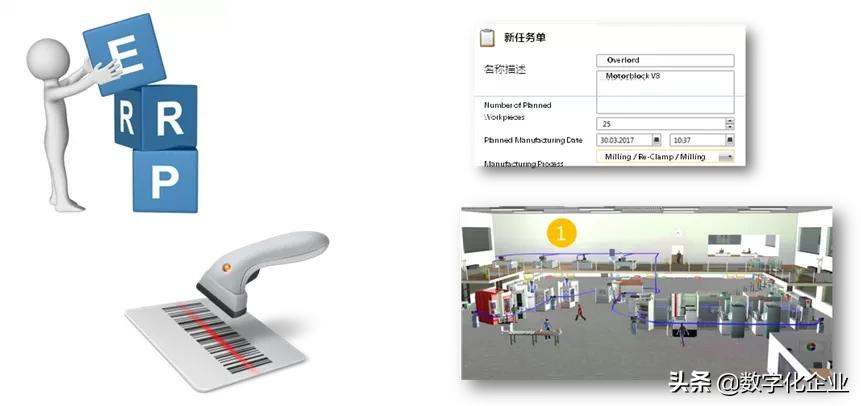
图42 创建/准备任务单
2)设置预调工件并分配RFID芯片(图43)
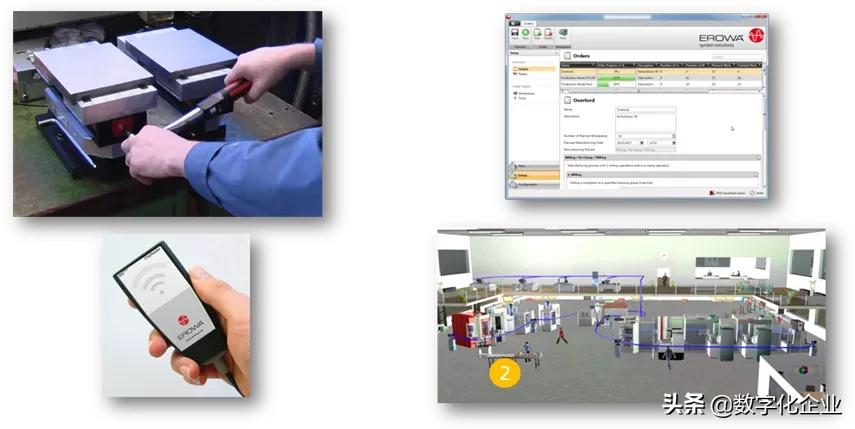
图43 分配RFID芯片
3)将托盘装入生产单元中,进行自动化生产,如图44所示。
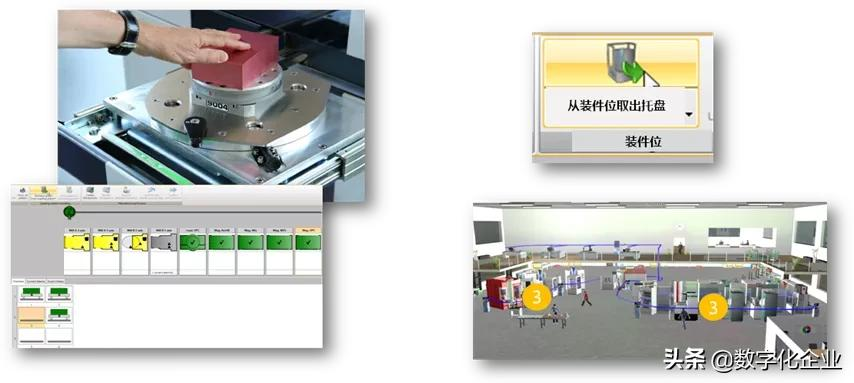
图44 自动化生产
4)集成三坐标测量机,进行质量控制,如图45所示。
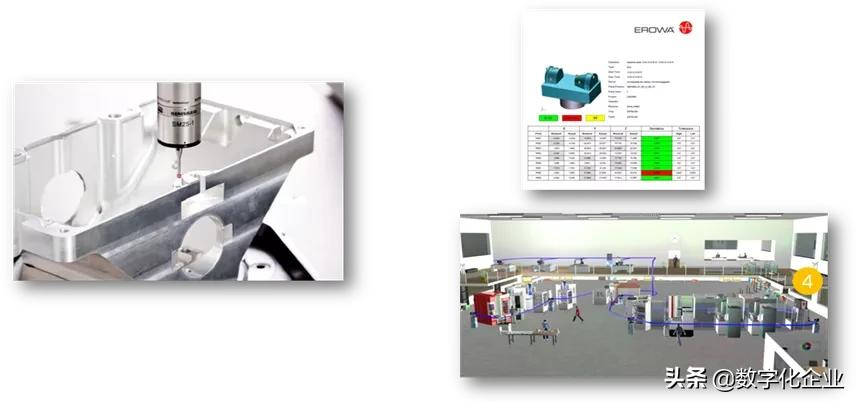
图45 质量控制
5)报告和反馈如图46所示,可采用AR/MR 交互实施,如图47所示。
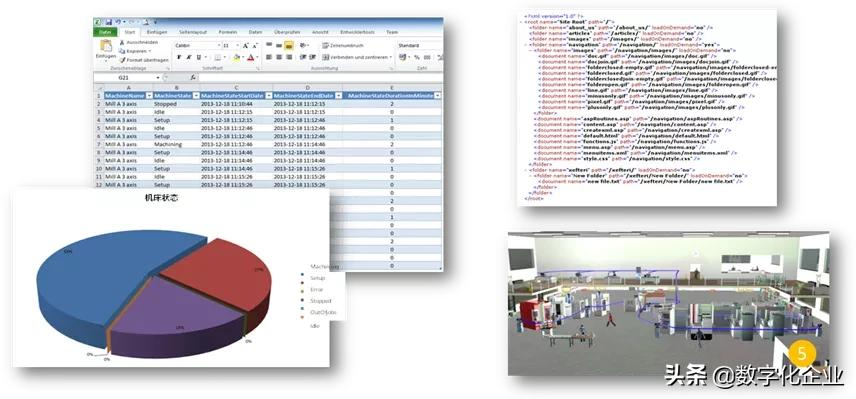
图46报告和反馈
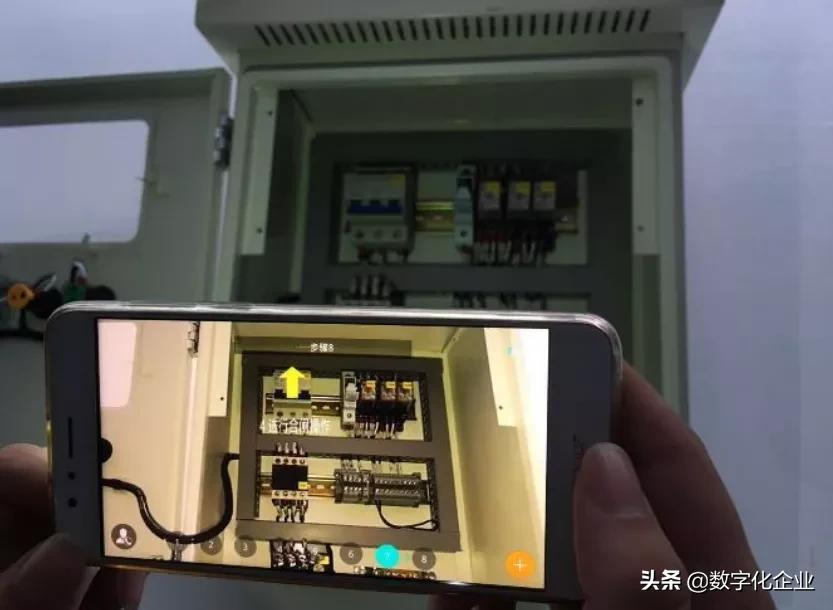
图47AR/MR 交互实施
小结
机器人+数控机床不是智能制造,由具有图像识别或力传感器的机器人和具有位移、振动、温度传感器的数控机床构成的系统才属于智能制造范畴。ERP+MES也不是智能制造,没有数据采集和设备状态反馈的系统是开环的和不可控的;智能制造是“数据→信息→优化→决策→价值创造”转化的闭环系统。互联网+WiFi更不是智能制造,它们是智能制造的基础设施,是手段,但绝非全部内容,离开物理的生产过程和实体设备,互联网什么也不能生产出来。自动化+数字化更不是智能制造,智能、智能、不能够感知和思考,不会交互和通信,就算不上智能。
智能制造从技术的角度看,传统制造是对物质的处理,将原料转化为产品,是基于经验的制造;智能制造是同时对物质和知识的处理,是基于科学(模型化)的制造。从企业运作的角度看,传统制造业是成本中心,通过大批量生产,降低成本,形成竞争力;智能制造是利润中心,通过客户化定制和协同获取最大利润。从最终用户的角度看,传统制造企业提供的是具体产品和有限的担保;而智能制造企业提供产品全生命周期的互联网服务,客户从购买产品转变为购买服务。智能制造不仅是技术的变革,而是生产模式、商务模式、经济体系、生活方式的变化。
参考文献
[1]张曙.混合加工挑战传统[J]. 现代制造现代金属加工[2015]12:9-11.
[2]Rombouts, M., et al., Surface Finish after Laser Metal Deposition. PhysicsProcedia, 2013.41(0): p. 810-814.
[3]Wang,Z., et al., Stereo vision based hybrid manufacturing process for precisionmetal parts. Precision Engineering, 2014(0).
- 还没有人评论,欢迎说说您的想法!